The EL appearance defect detection equipment for solar cell modules is an EL defect and appearance defect detection equipment customized by Yaohua Laser Technology for solar cell module manufacturers. Through this equipment, component related defects can be automatically determined; The use of electroluminescence and visual recognition to replace traditional detection methods not only saves manpower, but also accurately detects defects, reduces losses in the production process, and plays an important role in quality control of the photovoltaic manufacturing industry.
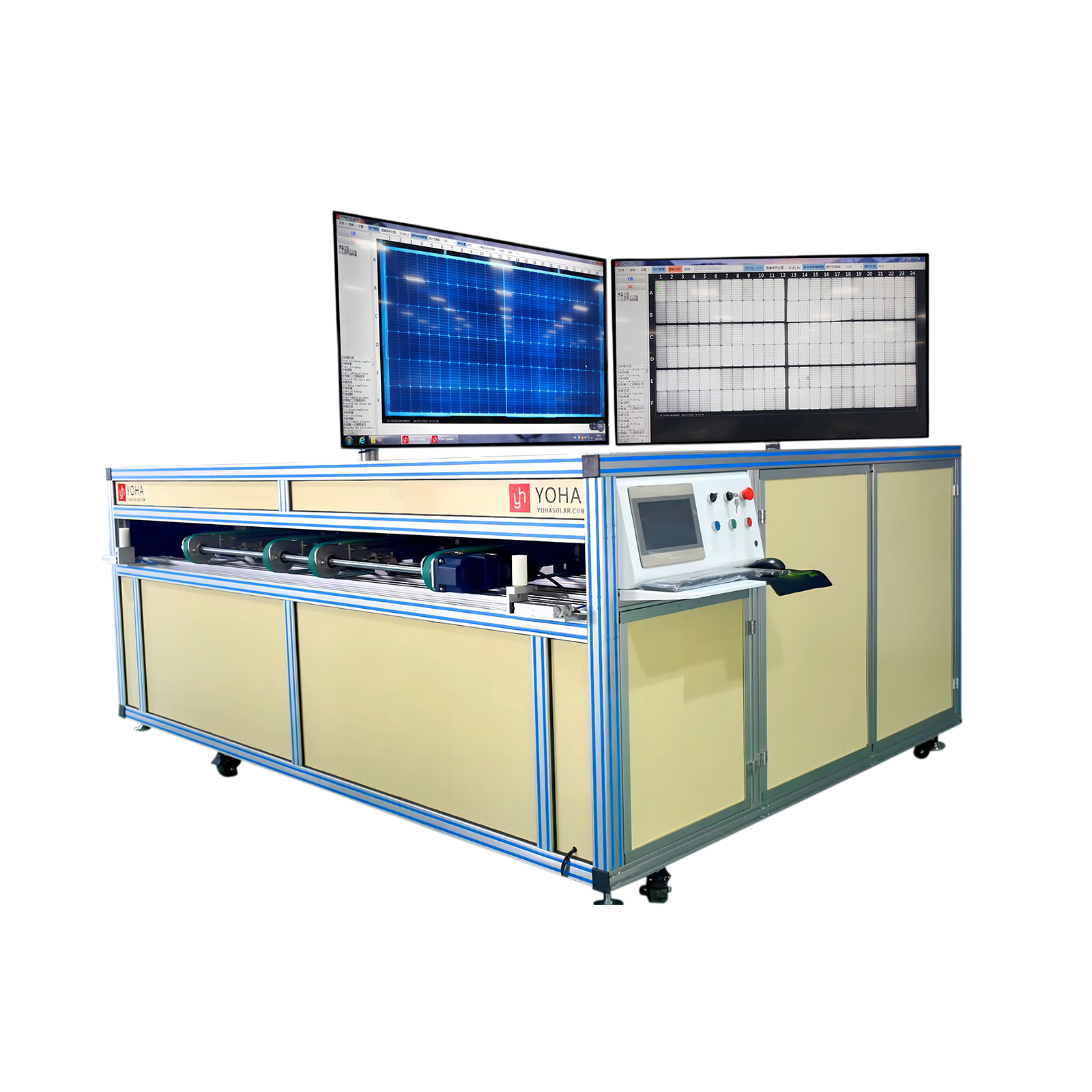
1、 Equipment structure and installation and debugging requirements
As shown in the above figure, the device is divided into two parts: the testing part and the display part.
Testing part: Box structure, including a testing line scanning camera and a testing strip light source.
Display section: includes 2 4K monitors, mainframe, keyboard and mouse, etc.
Installation requirements: The equipment utilizes the existing assembly line of the component factory and can be inserted into the assembly line for installation.
2、 Equipment workflow
The component enters station A - the component flows to station B - the device completes the collection of the EL appearance image on the front of the component - within 15 seconds, the software will automatically identify the location of the component appearance defect and label it for storage.
The equipment in the testing process does not affect the original pipeline function and is an independent testing system; Use your own sensors to collect signals for component detection.
The software can also feed back the OK/NG signal of the test results to the PLC of the pipeline for sorting.
3、 Equipment defect identification
Various defects such as hidden cracks, fragments, false soldering, black chips, broken grids, mixed gears, battery cell units, chipping, missing corners, scratches on battery cells, dirty battery cells, front of laminated components, residual flux, foreign objects on the glass surface of components, hollows, bubbles, glass scratches, and back of laminated components.
4、 Device software functions
Automatic image correction: Due to the inability of the assembly line to ensure complete uniform speed and component normalization, resulting in component image misalignment or distortion, the software can perform automatic image correction.
Automatic image storage: Images can be saved based on the current time and date, and the image size can be compressed and stored as a percentage.
Automatic barcode saving: There is a graphic scanner located on the device's back panel, which can recognize and save barcodes in specific areas of the back panel.
Database query: The software has a built-in database query function, allowing users to search for historical image defects by querying the appearance image of the component based on the date or barcode of the image.
keywords: